Developing xylem filters involves four simple steps as illustrated in the schematic. A detailed description of these steps has been provided below.
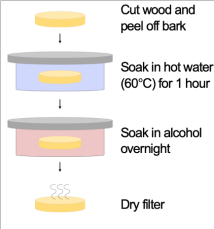
1. Wood sourcing: Cut a section of branch or the sapwood present in the trunk. Peel off the bark. The wood should be green and the cuttings should be stored in water to prevent drying.
2. Soaking in hot water to improve capacity: Xylem filters have a unique self-blocking behavior. Xylem is composed of loose hemicellulose fibers that dissolve in the water flowing through the filter and re-deposit on the membranes clogging them. This imposes an intrinsic limit on the filter’s shelf life. To mitigate self-blocking, xylem filters can be soaked in hot water at 60 deg C for 1 hour. The temperature and duration of treatment has been optimized for removing sufficient fibers to improve capacity, while mitigating damage to pit membranes to preserve rejection. This step might not be needed if the external contaminant load is high.
3. Dry preservation for extending shelf-life: Drying causes the membranes in the xylem to seal against the cell wall and at times, damages them. This results in poor flow rates and rejection performance and thus, short shelf-life of xylem filters. To improve shelf-life, two methods for preserving filters in a dry format can be followed:
i) Alcohol treatment: Soaking the cut filters in alcohol (ethanol, isopropanol, etc.) before drying preserves the structural integrity of membranes and provides a shelf-life of at least two years.
ii) Controlling filter thickness: The flow rates of dried filters depends strongly on filter thickness. By maintaining a filter thickness of ~0.25 inches, reasonable flow rates can be obtained. In order to mitigate the leakage of contaminants through damaged pit membranes and improve rejection, multiple thin filters can be stacked in series. This method is useful in areas where access to alcohol is difficult, although quality control might be difficult.
4. Drying: Filters can be either air-dried or in an oven at temperatures up to 45 deg C.